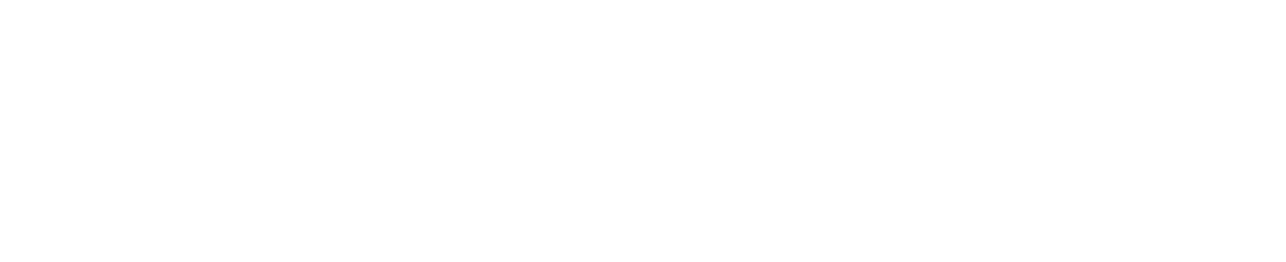
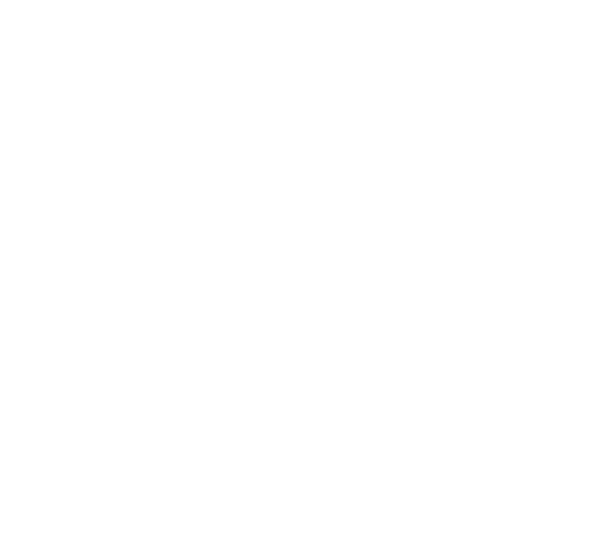
THE PACK THAT GOES AROUND COMES AROUND
In the same way you separate glass from plastic and paper from food waste in your recycling, the same needs to be done every time a piece of complex equipment or clothing, made from a bit of everything, is sent for recycling. Except, that doesn’t usually happen, in fact, the UK produces 206,500 tonnes of textile waste each year. That’s over 3kg of textile waste per person, per year. Of that, only 0.7kg is recycled or otherwise reused. 0.8kg is incinerated and 1.7kg goes to landfill. And to add insult to misery, much of the burning and landfill takes place overseas (around 60% of UK fabric waste is exported, equal to over 201,000 tonnes, annually) making us the 2nd largest exporter of fabric waste worldwide.
RUBBISH EFFORT
It is the complexity of their make-up that is partially responsible for these rubbish (pun intended? Ed.) figures.
Think about your jacket or pack; nylon fabric, polyester webbing, metal zipper teeth and plastic componentry (and if we were really serious about plastic waste, what about polyethylene from Nylon [stop thinking about stockings, Ed.]), short of cutting it down to its parts, how are you meant to separate it for recycling when it comes to the end of its life in the same way you’d separate your tins and glass bottles, especially if you don’t know what half the materials are, anyway?
Short answer: you don’t.
But what of the 0.7kg that gets recycled? Since they’re likely to be a mix of fabrics (most likely polymers unless you’re wearing a ventile jacket or a cotton rucksack, albeit most likely with polymer threads!) they can only be used to create a low-grade recycled product with a high degree of yet more wastage. That means to create more of the same grade of the original product, we must extract more resources (which if it’s a polymer, likely means crude oil).
CIRCULAR ECONOMY
So how can we get away from this unsustainable habit of use, half reuse, almost recycle and ultimately chuck in the ground or even burn?
One solution is the Circular Economy.
This is a concept whereby 100% of a product’s materials can be broken down and reused to create new, similar-grade products with close to zero waste.
This can be achieved by doing the same separating that you do at home but as we know, that’s a real pain and even the most committed don’t have a mass spectrometer to figure out which polymer they are chucking into the correct 150 different coloured bins they would need.
MONO-POLYMER
The other option is to manufacture a product using a single material (i.e. mono-polymer).
If you had a rucksack made from 100% nylon (fabric, zipper, buckles, webbing…everything) then all it would need to recycle is dump it in the right silo and away you go.
Except the technology to handle this kind of thing doesn’t exist…yet! Current estimates are we’re a decade away from the kind of large-scale recycling required to make this a reality (which is another way of saying affordable).
But that doesn’t mean it’s business as usual for the next ten years. Instead, now is the time to begin manufacturing products that are likely to reach the end of life, to coincide with this technology coming on stream.
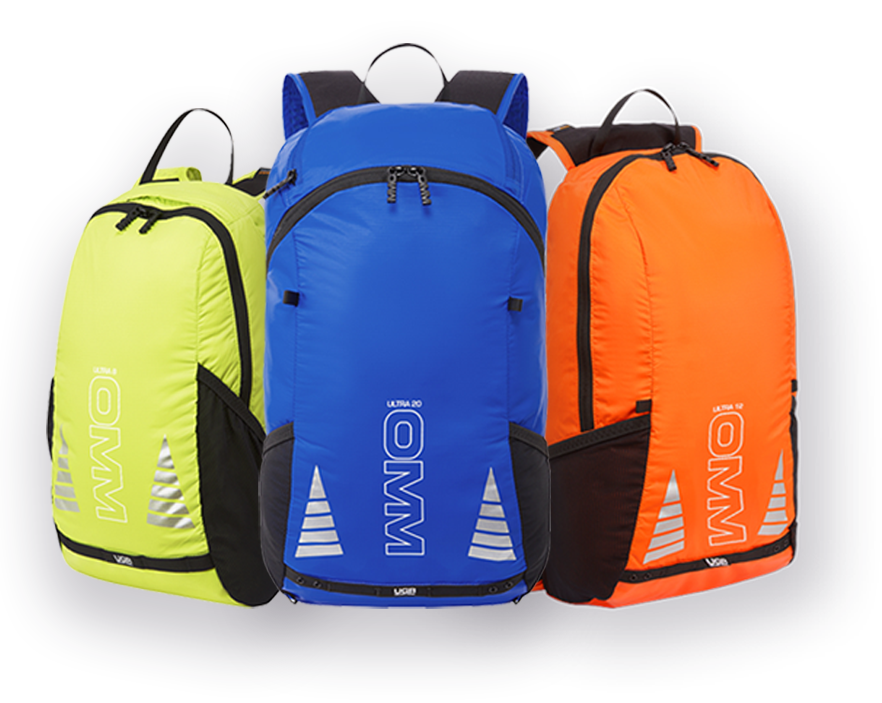
INFINIOMM
Enter INFINIOMM (Catchy, we know)
Our first step towards a more circular manufacture.
Products marked INFINIOMM have a mono-polymer construction, ready for efficient and effective recycling when they eventually reach the end of their usable life.
The first product to be released with the INFINIOMM technology is the updated Ultra Pack Range. Each pack is entirely constructed from high-quality Nylon; including zips, fabrics, webbing and toggles; the works!
No Extra Waste. No New Resources. Infinite Loop. Hopefully
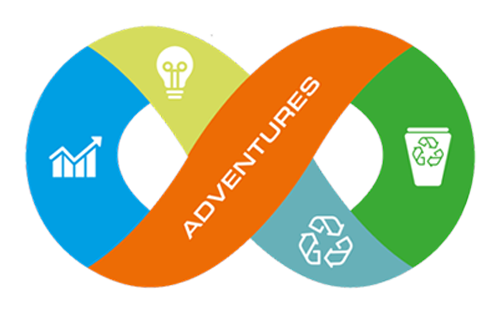